Coal gas
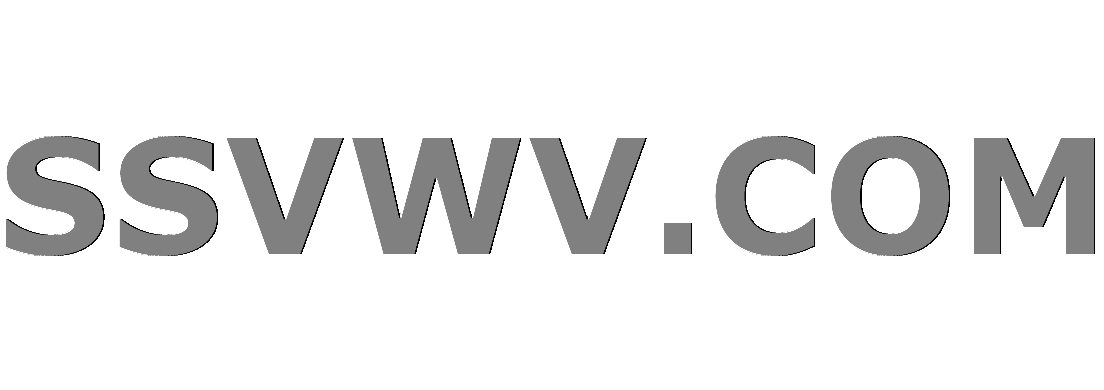
Multi tool use
Coal gas is a flammable gaseous fuel made from coal and supplied to the user via a piped distribution system. It is produced when coal is heated strongly in the absence of air. Town gas is a more general term referring to manufactured gaseous fuels produced for sale to consumers and municipalities.
Coal gas contains a variety of calorific gases including hydrogen, carbon monoxide, methane and volatile hydrocarbons together with small quantities of non-calorific gases such as carbon dioxide and nitrogen.
Prior to the development of natural gas supply and transmission—during the 1940s and 1950s in the United States and during the late 1960s and 1970s in Great Britain and Australia—virtually all gas for fuel and lighting was manufactured from coal. Town gas was supplied to households via municipally owned piped distribution systems.
Originally created as a by-product of the coking process, its use developed during the 19th and early 20th centuries tracking the industrial revolution and urbanization. By-products from the production process included coal tars and ammonia, which were important chemical feedstock for the dye and chemical industry with a wide range of artificial dyes being made from coal gas and coal tar. Facilities where the gas was produced were often known as a manufactured gas plant (MGP) or a gasworks.
The discovery of large reserves of natural gas in the North Sea off the English coast in 1965 [1][2] led to the expensive conversion or replacement of most of the UK's gas cookers and gas heaters, except in Northern Ireland, from the late 1960s onwards.
The production process is distinct, both physically and chemically,[clarification needed] from that used to create a range of gaseous fuels known variously as manufactured gas, syngas, hygas, Dowson gas, and producer gas. These gases are made by partial combustion of a wide variety of feed stocks in some mixture of air, oxygen, or steam, to reduce the latter to hydrogen and carbon dioxide although some destructive distillation may also occur.
Contents
1 Manufacturing processes
2 Gas for industrial use
3 War and post-war Britain
3.1 Changeover to natural gas
3.1.1 In popular culture
4 Gas production in Germany
5 Development of Pacific coast oil gas process
6 Layout of a typical gas plant
7 Issues in gas processing
8 WWI-interwar era developments
9 Post WWII: the decline of manufactured gas
10 Post WWII positive developments
11 Terminology in the UK
11.1 Manufacture
11.2 Composition
11.3 By-products
11.3.1 Coke
11.3.2 Coal tar
11.3.3 Sulfur
11.3.4 Ammonia
11.4 Structure of the industry
12 See also
13 References
13.1 Notes
13.2 Sources
14 Further reading
Manufacturing processes

Gas Works Park, Seattle, preserves most of the equipment for making coal gas. This is the only such plant surviving in the United States.
Manufactured gas can be made by two processes: carbonization or gasification. Carbonization refers to the devolatilization of an organic feedstock to yield gas and char. Gasification is the process of subjecting a feedstock to chemical reactions that produce gas.[3][4]
The first process used was the carbonization and partial pyrolysis of coal. The off gases liberated in the high-temperature carbonization (coking) of coal in coke ovens were collected, scrubbed and used as fuel. Depending on the goal of the plant, the desired product was either a high quality coke for metallurgical use, with the gas being a side product or the production of a high quality gas with coke being the side product. Coke plants are typically associated with metallurgical facilities such as smelters, and blast furnaces, while gas works typically served urban areas.
A facility used to manufacture coal gas, carburetted water gas (CWG), and oil gas is today generally referred to as a manufactured gas plant (MGP).
In the early years of MGP operations, the goal of a utility gas works was to produce the greatest amount of illuminating gas. The illuminating power of a gas was related to amount of soot-forming hydrocarbons (“illuminants”) dissolved in it. These hydrocarbons gave the gas flame its characteristic bright yellow color. Gas works would typically use oily bituminous coals as feedstock. These coals would give off large amounts of volatile hydrocarbons into the coal gas, but would leave behind a crumbly, low-quality coke not suitable for metallurgical processes. Coal or coke oven gas typically had a calorific value between 10 and 20 MJ/m³ (250-550 Btu/ft3 (std)); with values around 20 MJ/m³ (550 Btu/ft3 (std)) being typical.
The advent of electric lighting forced utilities to search for other markets for manufactured gas. MGPs that once produced gas almost exclusively for lighting shifted their efforts towards supplying gas primarily for heating and cooking, and even refrigeration and cooling.
Gas for industrial use

An illustration of typical polycyclic aromatic hydrocarbons. Source: NASA
Fuel gas for industrial use was made using producer gas technology. Producer gas is made by blowing air through an incandescent fuel bed (commonly coke or coal) in a gas producer. The reaction of fuel with insufficient air for total combustion produces carbon monoxide (CO); this reaction is exothermic and self-sustaining. It was discovered that adding steam to the input air of a gas producer would increase the calorific value of the fuel gas by enriching it with CO and hydrogen (H2) produced by water gas reactions. Producer gas has a very low calorific value of 3.7 to 5.6 MJ/m3 (99 to 150 BTU/cu ft); because the calorific gases CO/H2 are diluted with lots of inert nitrogen (from air) and carbon dioxide (CO2) (from combustion)
- 2C (s) + O2 → 2 CO (exothermic producer gas reaction)
- C (s) + H2O (g) → CO + H2 (endothermic water gas reaction)
- C + 2 H2O → CO2 + 2 H2 (endothermic)
- CO + H2O → CO2 + H2 (exothermic water gas shift reaction)
The problem of nitrogen dilution was overcome by the blue water gas (BWG) process, developed in the 1850s by Sir William Siemens. The incandescent fuel bed would be alternately blasted with air followed by steam. The air reactions during the blow cycle are exothermic, heating up the bed, while the steam reactions during the make cycle, are endothermic and cool down the bed. The products from the air cycle contain non-calorific nitrogen and are exhausted out the stack while the products of the steam cycle are kept as blue water gas. This gas is composed almost entirely of CO and H2, and burns with a pale blue flame similar to natural gas. BWG has a calorific value of 11 MJ/m3 (300 BTU/cu ft).
Blue water gas lacked illuminants; it would not burn with a luminous flame in a simple fishtail gas jet as existed prior to the invention of the Welsbach mantle in the 1890s. Various attempts were made to enrich BWG with illuminants from gas oil in the 1860s. Gas oil (an early form of gasoline) was the flammable waste product from kerosene refining, made from the lightest and most volatile fractions (tops) of crude oil.
In 1875 Thaddeus S. C. Lowe invented the carburetted water gas process. This process revolutionized the manufactured gas industry and was the standard technology until the end of manufactured gas era.[5] A CWG generating set consisted of three elements; a producer (generator), carburettor and a super heater connected in series with gas pipes and valves.[6]
During a make run, steam would be passed through the generator to make blue water gas. From the generator the hot water gas would pass into the top of the carburettor where light petroleum oils would be injected into the gas stream. The light oils would be thermocracked as they came in contact with the white hot checkerwork fire bricks inside the carburettor. The hot enriched gas would then flow into the superheater, where the gas would be further cracked by more hot fire bricks.[7]
War and post-war Britain

The post-war house building programme put gas at a disadvantage. Whereas electricity had long developed a national distribution grid, which enabled supplies to reach even small new housing developments, gas was still distributed only locally. Many new housing estates were beyond the reach of the gas main and the stringent Treasury rules about return on investment made extension of mains uneconomic. Electricity made inroads into the home heating market with underfloor heating and night storage heaters using cheap off-peak electricity supplies.
By the 1960s, manufactured gas, compared with its main rival in the energy market, electricity, was considered "nasty, smelly, dirty and dangerous" (to quote market research of the time) and seemed doomed to lose market share still further, except for cooking where its controllability gave it marked advantages over both electricity and solid fuel. The development of more efficient gas fires assisted gas to resist competition in the market for room heating. Concurrently a new market for whole house central heating by hot water was being developed by the oil industry and the gas industry followed suit. Gas warm air heating found a market niche in new local authority housing where low installation costs gave it an advantage. These developments, the realignment of managerial thinking away from commercial management (selling what the industry produced) to marketing management (meeting the needs and desires of customers) and the lifting of an early moratorium preventing nationalised industries from using television advertising, saved the gas industry for long enough to provide a viable market for what was to come.
Changeover to natural gas
In 1959 the Gas Council in Great Britain demonstrated that liquid natural gas (LNG) could be transported safely, efficiently and economically over long distances by sea. The Methane Pioneer shipped a consignment of LNG from Lake Charles, Louisiana, USA, to a new LNG terminal on Canvey Island, in the Thames estuary in Essex, England, and customers there were converted to use the new fuel. A 320-mile (510 km) long high-pressure trunk pipeline was built from London to Leeds.
The slow death of the town gas industry in the UK was signalled by the discovery of natural gas by the drilling rig Sea Gem, on 17 September 1965, some forty miles off Grimsby, over 8,000 feet (2,400 m) below the seabed. Subsequently, the North Sea was found to have many rich gas fields on both sides of the median line defining which nations should have rights over the reserves.
The Fuel Policy White Paper of 1967 (Cmd. 3438) pointed the industry in the direction of building up the use of natural gas speedily to 'enable the country to benefit as soon as possible from the advantages of this new indigenous energy source'. As a result, there was a 'rush to gas' for use in peak load electricity generation and in low grade uses in industry. The effects on the coal industry were very significant; not only did coal lose its market for town gas production, it came to be displaced from much of the bulk energy market also.
The exploitation of the North Sea gas reserves, entailing landing gas at Easington, Bacton and St Fergus made viable the building of a national distribution grid, of over 3,000 miles (4,800 km), consisting of two parallel and interconnected pipelines running the length of the country. All gas equipment in Great Britain (but not Northern Ireland) was converted (by the fitting of different-sized burner jets to give the correct gas/air mixture) from burning town gas to burn natural gas (mainly methane) over the period from 1967 to 1977 at a cost of about £100 million including the writing off of redundant town gas manufacturing plants. All the gas-using equipment of almost thirteen million domestic, four hundred thousand commercial, and sixty thousand industrial customers were converted. Many dangerous appliances were discovered in this exercise and were taken out of service. The UK town gas industry died in 1987 when operations ceased at the last town gas manufacturing plants in Northern Ireland (Belfast, Portadown and Carrickfergus; Carrickfergus gas works is now a restored gasworks museum).[8] The Portadown site has been cleared and is now the subject of a long-term experiment into the use of bacteria for the purpose of cleaning up contaminated industrial land. As well as requiring little processing before use, natural gas is non-toxic; the carbon monoxide (CO) in town gas made it extremely poisonous, accidental poisoning and suicide by gas being commonplace. Poisoning from natural gas appliances is only due to incomplete combustion, which creates CO, and flue leaks to living accommodation. As with town gas, a small amount of foul-smelling substance (mercaptan) is added to the gas to indicate to the user that there is a leak or an unlit burner, the gas having no odour of its own.
The organisation of the British gas industry adapted to these changes, first, by the Gas Act 1965 by empowering the Gas Council to acquire and supply gas to the twelve area boards. Then, the Gas Act 1972 formed the British Gas Corporation as a single commercial entity, embracing all the twelve area gas boards, allowing them to acquire, distribute and market gas and gas appliances to industrial commercial and domestic customers throughout the UK. In 1986, British Gas was privatised and dismembered and the Government no longer has any direct control over it.
During the era of North Sea gas, many of the original cast iron gas pipes installed in towns and cities for town gas were replaced by plastic.
As reported in the DTI Energy Review 'Our Energy Challenge' January 2006 North Sea gas resources have been depleted at a faster rate than had been anticipated and gas supplies for the UK are being sought from remote sources, a strategy made possible by developments in the technologies of pipelaying that enable the transmission of gas over land and under sea across and between continents. Natural gas is now a world commodity. Such sources of supply are exposed to all the risks of any import. There are still substantial coal reserves in the UK and this fact prompts the thought that at some time in the future, coal gas may once again be used as a reliable indigenous source of energy.
In popular culture
Monty Python parodied the conversion from coal to North Sea gas, and the jumping through hoops some encountered, in their "New Cooker Sketch," as part of the episode as began its second series in 1970.
Gas production in Germany
In many ways, Germany took the lead in coal gas research and carbon chemistry.
With the labours of Hofmann, the whole German chemical industry emerged.
Using the coal gas waste as feedstock, researchers developed new processes and synthesized
natural organic compounds such as vitamin C and aspirin.
The German economy relied on coal gas during the Second World War as petroleum shortages forced
Nazi Germany to develop the Fischer-Tropsch synthesis to produce synthetic fuel for aircraft and tanks.
Development of Pacific coast oil gas process
The Pacific coast process has significant problems with lampblack. 20 to 30 lb/1000 ft³ (300 to 500 g/m³) of oily soot can be created during combustion. Major pollution problems led to the passage of early state-level environmental legislation.
Layout of a typical gas plant
- 1880s Coal gasification plant.
- 1910 CWG plant

Coke oven at smokeless fuel plant, South Wales
Issues in gas processing
- Tar aerosols (tar extractors, condensers/scrubbers, Electrostatic precipitators in 1912)
- Light oil vapors (oil washing)
Naphthalene (oil/tar washing)
Ammonia gas (scrubbers)
Hydrogen sulfide gas (purifier boxes)
Hydrogen cyanide gas (purifier)
WWI-interwar era developments
- Loss of high-quality gas oil (used as motor fuel) and feed coke (diverted for steelmaking) leads to massive tar problems. CWG (carburetted water gas) tar is less valuable than coal gasification tar as a feed stock. Tar-water emulsions are uneconomical to process due to unsellable water and lower quality by products.
- CWG tar is full of lighter polycyclic aromatic hydrocarbons, good for making pitch, but poor in chemical precursors.
- Various "back-run" procedures for CWG generation lower fuel consumption and help deal with issues from the use of bitumious coal in CWG sets.
- Development of high-pressure pipeline welding encourages the creation of large municipal gas plants and the consolidation of the MG industry. Sets the stage for rise of natural gas.
- Electric lighting replaces gaslight. MG industry peak is sometime in the mid-1920s.
- 1936 or so. Development of Lurgi gasifier. Germans continue work on gasification/synfuels due to oil shortages.

Ruins of the German synthetic petrol plant (Hydrierwerke Pölitz – Aktiengeselschaft) in Police, Poland
- The Public Utility Holding Company Act of 1935, in the US, forces break up of integrated coke and gas companies in the United States.
Fischer-Tropsch process for synthesis of liquid fuels from CO/H
2 gas.
Haber-Bosch ammonia process creates a large demand for industrial hydrogen.
Post WWII: the decline of manufactured gas
- Development of natural gas industry. NG is 37 MJ/m³
- Petrochemicals kill much of the value coal tar as a source of chemical feed stocks. (BTX, Phenols, Pitch)
- Decline in creosote use for wood preserving.
- Direct coal/natural gas injection reduces demand for metallurgical coke. 25 to 40% less coke is needed in blast furnaces.
- BOF and EAF processes obsolete cupola furnaces. Reduce need for coke in recycling steel scrap. Less need for fresh steel/iron.
Cast iron & steel are replaced with aluminum and plastics.
Phthalic anhydride production shifts from catalytic oxidation of naphthalene to the o-xylol process.
Post WWII positive developments
- Catalytic upgrading of gas by use of hydrogen to react with tarry vapors in the gas
- The decline of coke making in the US leads to a coal tar crisis since coal tar pitch is vital for the production of carbon electrodes for EAF/Aluminum. US now has to import coal tar from China
- Development of process to make methanol via hydrogenation of CO/H2 mixtures.
- Mobil M-gas process for making gasoline from methanol
SASOL coal process plant in South Africa.- Direct hydrogenation of coal into liquid and gaseous fuels
Terminology in the UK
In British usage, coal gas specifically means gas made by the destructive distillation of coal. The term is not applied to other coal-derived gases, such as water gas, producer gas and syngas. United States usage may be different.
Coal gas was introduced in the UK in the 1790s as an illuminating gas by the Scottish inventor William Murdoch and became very widely used for lighting, cooking, heating and powering gas engines.
Manufacture
Coal was heated in a retort and the crude gas was passed through a condenser to remove tar and a scrubber to remove other impurities. The residue remaining in the retort was coke.
Composition
The composition of coal gas varied according to the type of coal and the temperature of carbonisation. Typical figures were:
hydrogen 50%
methane 35%
carbon monoxide 10%
ethylene 5%
In a plain burner, only the ethylene produced a luminous flame but the light output could be greatly increased by using a gas mantle.
By-products
The by-products of coal gas manufacture included coke, coal tar, sulfur and ammonia and these were all useful products.
Dyes, medicines such as sulfa drugs, saccharine, and dozens of organic compounds are made from coal tar.[citation needed]
Coke
Coke is used as a smokeless fuel and for the manufacture of water gas and producer gas.
Coal tar
Coal tar was subjected to fractional distillation to recover various products, including
tar, for roads
benzole, a motor fuel
creosote, a wood preservative
phenol, used in the manufacture of plastics
cresols, disinfectants
Sulfur
Used in the manufacture of sulfuric acid
Ammonia
Used in the manufacture of fertilisers
Structure of the industry
Coal gas was initially manufactured by independent companies but many of these later became municipal services. Both the private and the municipal companies were nationalised under the Gas Act 1948 and further re-structuring took place under the Gas Act 1972. For further details see British Gas plc.
Apart from in the steel industry's coke oven's by products plants, coal gas is no longer made in the UK. It was replaced first by gas made from oil and later by natural gas from the North Sea.
See also
- Damp (mining)
- Environmental remediation
- Gas lighting
- Gas Works Park
- Gasifier
- Gasometer
- Gasworks
- History of manufactured gas
- Illuminating gas
- Mond gas
- Wood gas
References
Notes
^ National Gas Museum: Gas industry timeline
^ West Sole Gas Fields
^ Beychok, M.R., Process and environmentals technology for producing SNG and liquid fuels, U.S, EPA report EPA-660/2-2-75-011, May 1975
^ Beychok, M.R., Coal gasification and the phenolsolvan process, American Chemical Society 168th National Meeting, Atlantic City, September 1974
^ "The Introduction of Water Gas in the United States" (Google Books excerpt). The Baltimore Gas and Electric News. Consolidated Gas, Electric Light, and Power Company of Baltimore. 5 (6): 383. 1916..mw-parser-output cite.citationfont-style:inherit.mw-parser-output qquotes:"""""""'""'".mw-parser-output code.cs1-codecolor:inherit;background:inherit;border:inherit;padding:inherit.mw-parser-output .cs1-lock-free abackground:url("//upload.wikimedia.org/wikipedia/commons/thumb/6/65/Lock-green.svg/9px-Lock-green.svg.png")no-repeat;background-position:right .1em center.mw-parser-output .cs1-lock-limited a,.mw-parser-output .cs1-lock-registration abackground:url("//upload.wikimedia.org/wikipedia/commons/thumb/d/d6/Lock-gray-alt-2.svg/9px-Lock-gray-alt-2.svg.png")no-repeat;background-position:right .1em center.mw-parser-output .cs1-lock-subscription abackground:url("//upload.wikimedia.org/wikipedia/commons/thumb/a/aa/Lock-red-alt-2.svg/9px-Lock-red-alt-2.svg.png")no-repeat;background-position:right .1em center.mw-parser-output .cs1-subscription,.mw-parser-output .cs1-registrationcolor:#555.mw-parser-output .cs1-subscription span,.mw-parser-output .cs1-registration spanborder-bottom:1px dotted;cursor:help.mw-parser-output .cs1-hidden-errordisplay:none;font-size:100%.mw-parser-output .cs1-visible-errorfont-size:100%.mw-parser-output .cs1-subscription,.mw-parser-output .cs1-registration,.mw-parser-output .cs1-formatfont-size:95%.mw-parser-output .cs1-kern-left,.mw-parser-output .cs1-kern-wl-leftpadding-left:0.2em.mw-parser-output .cs1-kern-right,.mw-parser-output .cs1-kern-wl-rightpadding-right:0.2em
^ Proceedings of the American Gas Light Association ... By American Gas Light Association, 1881 p.117 https://books.google.com/books?id=OSNLAAAAMAAJ&pg=PA116
^ Power: devoted to the generation and transmission of power, Volume 26 1906 p.686 https://books.google.com/books?id=DcEfAQAAMAAJ&pg=PA687&lpg=PA687
^ "Flame Gasworks". www.flamegasworks.co.uk.
Sources
- Everard, Stirling (1949). The History of the Gas Light and Coke Company 1812–1949. London: Ernest Benn Limited. (Reprinted 1992, London: A&C Black (Publishers) Limited for the London Gas Museum.
ISBN 0-7136-3664-5.)
Further reading
Barty-King, H. (1985). New Flame: How Gas changed the commercial, domestic and industrial life in Britain from 1783 to 1984. Tavistock: Graphmitre. ISBN 0-948051-00-0.
Peebles, Malcolm W. H. (1980). Evolution of the Gas Industry. London and Basingstoke: Macmillan. ISBN 0-333-27971-9.
Fressoz, J. B. (2007). "The gas lighting controversy, technological risk, expertise and regulation in Paris and London, 1815-1850". Journal of Urban History. 33 (5): 729–755. doi:10.1177/0096144207301418.
Fb,3u hCW85vWa6PFYgmRfZeh,3lm,PH4nQlehOEUNP,9HCALdjxsKps3YTEkzBZlCwNMx24v